کیفیت خودرو با آبکاری یکی از عوامل کلیدی در موفقیت صنعت خودروسازی به شمار میآید و تأثیر مستقیم بر رضایت مشتریان، ایمنی و عملکرد خودرو دارد. با افزایش رقابت در بازار جهانی و تغییر نیازهای مصرفکنندگان، تولیدکنندگان خودرو ناگزیر به بهبود مستمر کیفیت محصولات خود هستند. این امر نه تنها شامل استفاده از مواد اولیه با کیفیت و فناوریهای پیشرفته در طراحی و ساخت خودروها میشود، بلکه به کارگیری تکنیکهای نوین در فرآیندهای تولید نیز از اهمیت بالایی برخوردار است.
یکی از این تکنیکهای مؤثر که به طور فزایندهای در صنعت خودروسازی مورد توجه قرار گرفته، آبکاری است. آبکاری با ایجاد لایههای محافظتی بر روی قطعات مختلف خودرو، میتواند به بهبود مقاومت در برابر زنگ زدگی، سایش و آسیبهای محیطی کمک کند.
این فرآیند همچنین میتواند به افزایش زیبایی ظاهری خودرو و بهبود عملکرد مکانیکی قطعات کمک کند. با توجه به پیشرفتهای روزافزون در تکنیکهای آبکاری، از جمله روشهای الکتروپلاستیک و آبکاری نانو، این تکنیکها به عنوان راهکارهایی مؤثر برای افزایش کیفیت و دوام خودروها در نظر گرفته میشوند.
مفهوم آبکاری و فرآیندهای آن
آبکاری به فرآیند پوشش دهی سطح یک جسم با لایهای از فلز یا ماده دیگر به منظور بهبود خواص فیزیکی و شیمیایی آن اشاره دارد. آبکاری معمولاً با استفاده از روش های الکتروکیمیایی انجام میشود که در آن یک الکترود منفی (قطعه مورد نظر) در محلول حاوی یونهای فلزی قرار میگیرد و با اعمال جریان الکتریکی، یونهای فلزی به سطح قطعه منتقل و رسوب میکنند.
این لایه پوششی میتواند ویژگیهایی مانند افزایش مقاومت در برابر زنگ زدگی، بهبود ظاهر، کاهش سایش و افزایش دوام را به قطعه اضافه کند. فرآیندهای آبکاری شامل روشهای مختلفی هستند، از جمله آبکاری الکتروپلاستیک، آبکاری غوطهوری، آبکاری پودری و آبکاری با استفاده از فناوری نانو، که هر یک مزایا و کاربردهای خاص خود را دارند.
تاریخچه آبکاری در صنعت خودروسازی
تاریخچه آبکاری در صنعت خودروسازی به اوایل قرن بیستم برمیگردد، زمانی که تولیدکنندگان خودرو به دنبال روشهایی برای بهبود کیفیت و دوام قطعات خودرو بودند. تاریخچه آبکاری با استفاده از روشهای ساده و ابتدایی آغاز شد که معمولاً شامل پوششدهی با نیکل یا کروم بود تا قطعات خودرو در برابر زنگزدگی و سایش محافظت شوند.
با گذشت زمان و پیشرفت فناوری، تکنیکهای آبکاری بهبود یافته و به روش های مدرن تری مانند آبکاری الکتروپلاستیک و آبکاری نانو توسعه یافتند که به تولیدکنندگان این امکان را میدهد که قطعاتی با کیفیت بالاتر و دوام بیشتر تولید کنند.
امروزه، آبکاری به عنوان یک بخش حیاتی از فرآیند تولید خودرو شناخته میشود و به تولیدکنندگان کمک میکند تا خودروهایی با کیفیت بالا، ایمنی بیشتر و جذابیت ظاهری بالاتر به بازار عرضه کنند. با توجه به نیاز روزافزون به کاهش وزن خودروها و بهبود عملکرد آنها، تکنیکهای نوین آبکاری به یک ابزار مهم در ارتقای کیفیت و بهرهوری در صنعت خودروسازی تبدیل شدهاند.
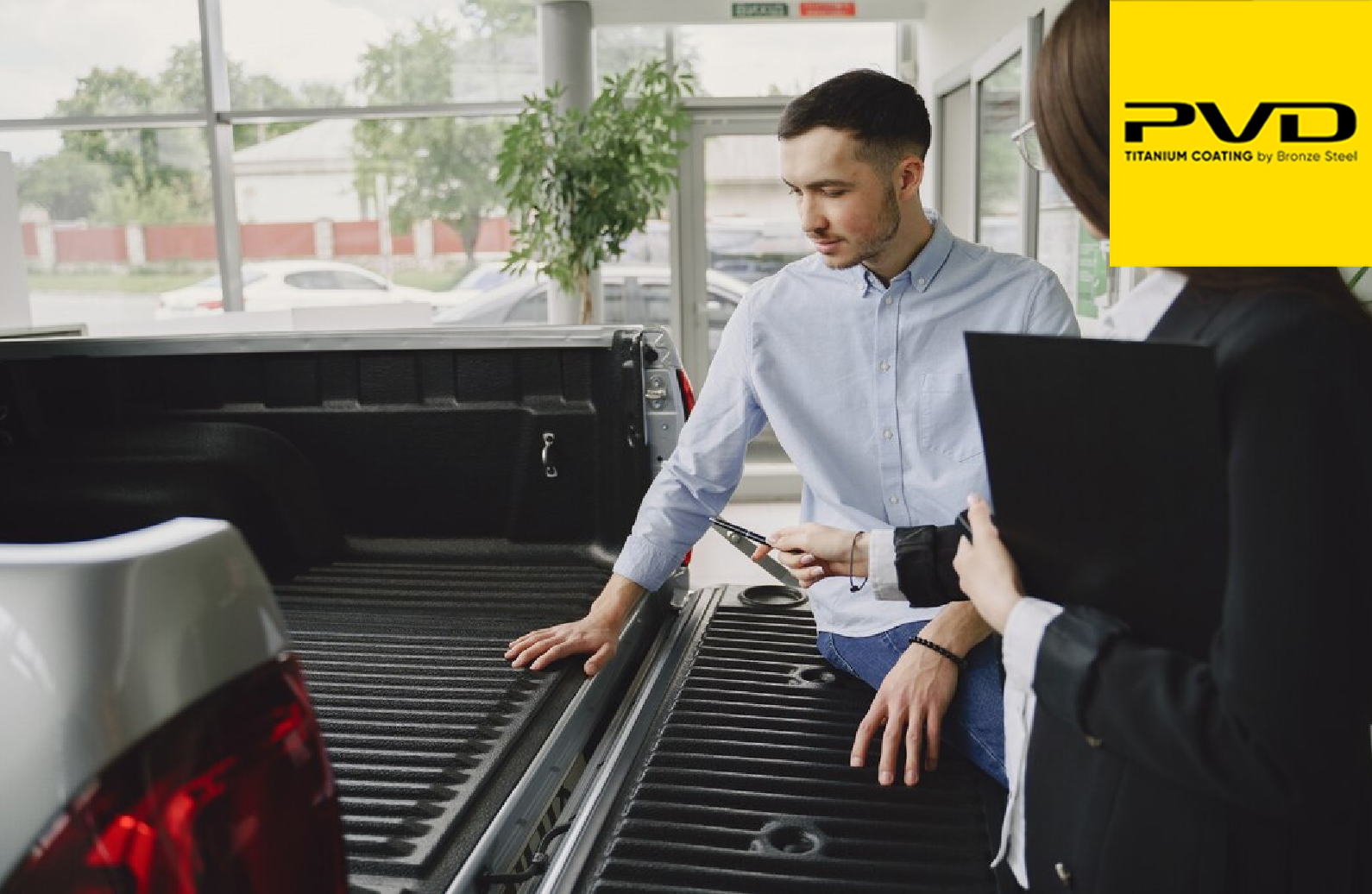
انواع تکنیک های آبکاری در صنعت خودروسازی
در صنعت خودروسازی، تکنیکهای مختلف آبکاری به منظور بهبود کیفیت، دوام و زیبایی قطعات خودرو استفاده میشوند. در ادامه، به معرفی و توضیح انواع تکنیکهای آبکاری متداول در این صنعت میپردازیم:
آبکاری الکتروپلاستیک یکی از محبوبترین روشهای آبکاری است که در آن با استفاده از جریان الکتریکی، لایهای از فلز بر روی سطح قطعه رسوب میشود. آبکاری الکتروپلاستیک معمولاً شامل استفاده از محلولهای حاوی یونهای فلزی است که به قطعهای که به عنوان کاتد عمل میکند، منتقل میشوند.
این روش به تولید قطعاتی با کیفیت بالا، ضخامت کنترلشده و مقاومت عالی در برابر زنگزدگی و سایش کمک میکند. در صنعت خودروسازی، آبکاری الکتروپلاستیک معمولاً برای پوششدهی قطعاتی مانند رینگهای چرخ، سیستمهای ترمز و قطعات داخلی خودرو استفاده میشود.
در روش آبکاری غوطهوری، قطعه مورد نظر به طور کامل در محلول حاوی مواد پوششی غوطهور میشود. آبکاری غوطهوری معمولاً برای پوششدهی با لایههای ضخیمتر و مواد غیر فلزی مانند رنگ یا پلاستیک استفاده میشود. پس از غوطهوری، قطعه از محلول خارج شده و به طور طبیعی یا در کوره خشک میشود.
آبکاری غوطهوری به دلیل سادگی و سرعت بالا در فرآیند، در صنایع مختلف از جمله خودروسازی برای پوششدهی قطعات بدنه و محافظت از آنها در برابر زنگزدگی و آسیبهای محیطی کاربرد دارد.
آبکاری پودری یک روش مدرن و دوستدار محیط زیست است که در آن از پودرهای خشک به عنوان پوشش استفاده میشود. در آبکاری پودری ، پودر پوششی به صورت یکنواخت بر روی سطح قطعه پاشیده میشود و سپس با استفاده از حرارت، پودر به یک لایه محکم و یکنواخت تبدیل میشود.
این روش به دلیل مقاومت بالا در برابر زنگزدگی، سایش و UV و همچنین تنوع رنگ و بافت، در صنعت خودروسازی برای پوششدهی بدنه خودروها، قطعات داخلی و خارجی و تجهیزات جانبی بسیار محبوب است.
آبکاری نیکل کروم ترکیبی از دو لایه آبکاری نیکل و کروم است که به طور معمول برای بهبود زیبایی و مقاومت در برابر زنگزدگی و سایش استفاده میشود. لایه نیکل به عنوان یک لایه زیرین عمل میکند که به چسبندگی بهتر و مقاومت در برابر زنگزدگی کمک میکند، در حالی که لایه کروم به دلیل درخشش و زیبایی خود، جذابیت ظاهری را افزایش میدهد. آبکاری نیکل-کروم در صنعت خودروسازی برای قطعاتی مانند رینگهای چرخ، دستگیرهها و قطعات تزئینی استفاده میشود.
- آبکاری با استفاده از فناوری نانو
آبکاری با استفاده از فناوری نانو به فرآیندهایی اشاره دارد که در آن از نانوذرات برای ایجاد لایههای پوششی با خواص خاص استفاده میشود. آبکاری با استفاده از فناوری نانو میتواند به بهبود ویژگیهای سطحی مانند مقاومت در برابر سایش، زنگزدگی و حرارت کمک کند.
نانوذرات میتوانند به صورت ترکیبی با فلزات دیگر یا به تنهایی استفاده شوند تا خواص بهتری را به قطعه مورد نظر اضافه کنند. آبکاری با استفاده از فناوری نانو در صنایع خودروسازی برای افزایش دوام قطعات و بهبود عملکرد آنها به کار میرود و میتواند به کاهش وزن خودروها و افزایش کارایی آنها کمک کند.
آبکاری با طلا و نقره معمولاً برای جواهرات و قطعات تزئینی خودروها استفاده میشود. آبکاری با طلا و نقره به دلیل زیبایی و درخشش خاص این فلزات، جذابیت ظاهری را افزایش میدهد و میتواند به عنوان یک لایه محافظ نیز عمل کند. آبکاری با طلا و نقره بیشتر در بخشهای داخلی خودرو مانند داشبورد، دستگیرهها و سایر قطعات تزئینی به کار میرود.
- آبکاری آنودایزینگ (Anodizing)
آنودایزینگ یک روش آبکاری الکتروشیمیایی است که معمولاً برای آلومینیوم استفاده میشود. در این فرآیند آبکاری، اکسید آلومینیوم بر روی سطح فلز ایجاد میشود که به افزایش مقاومت در برابر خوردگی و سایش کمک میکند و همچنین میتواند به عنوان یک لایه رنگی عمل کند. این روش در صنعت خودروسازی به ویژه برای قطعات آلومینیومی و اجزای سبک وزن که نیاز به مقاومت بالا دارند، کاربرد دارد.
این تکنیکها به تولیدکنندگان خودرو کمک میکنند تا کیفیت و دوام قطعات خود را افزایش دهند و در عین حال زیبایی ظاهری و عملکرد خودروها را بهبود بخشند.
مزایای آبکاری در صنعت خودرو
مزایای آبکاری در صنعت خودرو به طور قابل توجهی به کیفیت و عملکرد خودروها کمک میکند. در ادامه به توضیح هر یک از این مزایا میپردازیم:
- افزایش مقاومت در برابر زنگ زدگی و اکسیداسیون
آبکاری یکی از مؤثرترین روشها برای افزایش مقاومت قطعات خودرو در برابر زنگزدگی و اکسیداسیون است. با ایجاد یک لایه محافظ بر روی سطح فلز، آبکاری مانع از تماس مستقیم فلز با رطوبت و عوامل خورنده محیطی میشود.
آبکاری به ویژه در قطعاتی که در معرض شرایط جوی نامساعد و رطوبت قرار دارند، بسیار مهم است. به عنوان مثال، آبکاری نیکل و کروم معمولاً برای بدنه خودرو و اجزای سیستمهای ترمز استفاده میشود تا از زنگزدگی و آسیبهای ناشی از اکسیداسیون جلوگیری کند. این ویژگی به افزایش عمر مفید قطعات و کاهش هزینههای تعمیر و نگهداری کمک میکند.
- بهبود استحکام و دوام قطعات
آبکاری میتواند به طور قابل توجهی استحکام و دوام قطعات خودرو را افزایش دهد. لایههای آبکاری شده معمولاً دارای خواص فیزیکی و مکانیکی بهتری هستند که میتوانند مقاومت در برابر سایش، ضربه و فشار را افزایش دهند.
به عنوان مثال، آبکاری نیکل میتواند به تقویت ساختار فلز زیرین کمک کند و در نتیجه، مقاومت قطعه در برابر آسیبهای مکانیکی را افزایش دهد. این امر به ویژه در قطعاتی که تحت بارهای سنگین قرار دارند، مانند سیستمهای تعلیق و محورهای چرخ، اهمیت دارد و میتواند به کاهش احتمال شکست و خرابی قطعات کمک کند.
- افزایش زیبایی و جذابیت ظاهری
آبکاری میتواند به طور چشمگیری زیبایی و جذابیت ظاهری خودروها را افزایش دهد. لایههای آبکاری شده معمولاً دارای درخشندگی و رنگهای زیبا هستند که میتوانند به طراحی خودرو جلوهای خاص ببخشند.
برای مثال، آبکاری با طلا یا نقره معمولاً برای قطعات تزئینی داخلی و خارجی خودروها استفاده میشود تا جذابیت ظاهری آنها را افزایش دهد. همچنین، آبکاری پودری و الکتروپلاستیک به تولید رنگهای متنوع و پوششهای بافتدار کمک میکند که میتواند به طراحی مدرن و جذاب خودروها افزوده شود.
- کاهش سایش و اصطکاک
آبکاری میتواند به کاهش سایش و اصطکاک بین قطعات متحرک خودرو کمک کند. با ایجاد یک لایه نرمتر و صافتر بر روی سطح قطعات، آبکاری میتواند تماس بین قطعات را بهبود بخشد و در نتیجه سایش و اصطکاک را کاهش دهد.
ویژگی کاهش سایش و اصطکاک به ویژه در موتور خودرو و سیستمهای انتقال قدرت اهمیت دارد، جایی که کاهش اصطکاک میتواند به بهبود عملکرد و کارایی موتور کمک کند. همچنین، کاهش سایش باعث افزایش عمر مفید قطعات و کاهش نیاز به تعمیرات و نگهداری میشود، که در نهایت به بهبود بهرهوری و کاهش هزینهها منجر میشود.
این مزایا به طور کلی باعث افزایش کیفیت و کارایی خودروها میشوند و به تولیدکنندگان کمک میکنند تا محصولات بهتری را به بازار عرضه کنند.
کاربردهای آبکاری در صنعت خودروسازی
آبکاری در صنعت خودروسازی به طور گسترده ای برای بهبود کیفیت و عملکرد قطعات مختلف استفاده میشود. در ادامه به بررسی کاربردهای آبکاری در سه دسته اصلی: قطعات بدنه، قطعات داخلی و قطعات مکانیکی میپردازیم.
- آبکاری قطعات بدنه (مانند دربها و کاپوت)
آبکاری قطعات بدنه خودرو، از جمله دربها و کاپوت، به عنوان یکی از مهمترین کاربردهای آبکاری در صنعت خودروسازی شناخته میشود. قطعات بدنه به طور مستقیم در معرض عوامل محیطی مانند رطوبت، باران، آفتاب و گرد و غبار قرار دارند و به همین دلیل نیاز به محافظت در برابر زنگزدگی و آسیبهای ناشی از اکسیداسیون دارند.
آبکاری با استفاده از فلزاتی مانند نیکل و کروم، لایهای محافظ بر روی سطح این قطعات ایجاد میکند که به افزایش مقاومت در برابر زنگزدگی و سایش کمک میکند. همچنین، این لایه میتواند زیبایی ظاهری خودرو را با ایجاد درخشش و رنگهای متنوع افزایش دهد. به علاوه، آبکاری میتواند به کاهش وزن خودرو کمک کند، زیرا با استفاده از مواد سبک و مقاوم، میتوان ساختار بدنه را تقویت کرد. در نتیجه، آبکاری قطعات بدنه به بهبود ایمنی، دوام و جذابیت ظاهری خودرو کمک میکند.
- آبکاری قطعات داخلی (مانند داشبورد و دستگیرهها)
آبکاری در قطعات داخلی خودرو، مانند داشبورد، دستگیرهها و سایر اجزای تزئینی، به منظور بهبود زیبایی و کیفیت این قطعات انجام میشود. داشبورد و دستگیرهها به طور مستقیم با کاربران در ارتباط هستند و احساس راحتی و کیفیت آنها میتواند تأثیر زیادی بر تجربه کاربری داشته باشد.
آبکاری با استفاده از فلزات با کیفیت و بافتهای خاص، میتواند جلوهای زیبا و لوکس به داخل خودرو ببخشد. به عنوان مثال، آبکاری نیکل یا کروم برای دستگیرهها و کنترلها باعث افزایش درخشش و جذابیت ظاهری آنها میشود. همچنین، آبکاری میتواند به افزایش مقاومت در برابر سایش و خراشیدگی کمک کند، به ویژه در نقاطی که بیشتر در معرض استفاده قرار دارند. علاوه بر این، آبکاری میتواند به عنوان یک لایه محافظ در برابر گرد و غبار و آلودگی عمل کند و به تمیزی و نگهداری آسانتر قطعات داخلی کمک کند.
- آبکاری قطعات مکانیکی (مانند پیستونها و محورهای چرخ)
آبکاری در قطعات مکانیکی خودرو، مانند پیستونها، محورهای چرخ و سایر اجزای متحرک، به منظور بهبود عملکرد و افزایش دوام این قطعات انجام میشود. قطعاتی مانند پیستونها و محورهای چرخ تحت بارهای سنگین و شرایط سخت کاری قرار دارند و بنابراین نیاز به محافظت و تقویت دارند.
آبکاری میتواند به افزایش مقاومت در برابر سایش و اصطکاک کمک کند. به عنوان مثال، آبکاری نیکل یا کروم بر روی پیستونها میتواند به کاهش اصطکاک بین پیستون و سیلندر کمک کند، که در نهایت به بهبود عملکرد موتور و کاهش مصرف سوخت منجر میشود. همچنین، آبکاری میتواند به تقویت ساختار قطعات و افزایش عمر مفید آنها کمک کند، که در نتیجه نیاز به تعمیرات و نگهداری را کاهش میدهد. در محورهای چرخ نیز، آبکاری میتواند به افزایش مقاومت در برابر زنگزدگی و سایش کمک کند، تا عملکرد بهینه و ایمنی خودرو در شرایط مختلف تضمین شود.
تأثیر آبکاری بر عملکرد خودرو
آبکاری به عنوان یک فرآیند حیاتی در صنعت خودروسازی، تأثیر قابل توجهی بر عملکرد خودرو دارد. یکی از مهمترین تأثیرات آبکاری، افزایش مقاومت قطعات در برابر سایش و زنگزدگی است. با ایجاد لایههای محافظ بر روی قطعات مختلف خودرو، مانند پیستونها، محورهای چرخ و بدنه، آبکاری میتواند به کاهش اصطکاک و سایش بین قطعات متحرک کمک کند.
این امر نه تنها به بهبود عملکرد موتور و سیستمهای انتقال قدرت منجر میشود، بلکه میتواند به افزایش عمر مفید قطعات و کاهش نیاز به تعمیر و نگهداری نیز کمک کند. در نتیجه، خودروهایی که از تکنیکهای آبکاری پیشرفته بهره میبرند، معمولاً کارایی بالاتری دارند و به طور کلی از نظر عملکرد قابل اعتمادتر هستند.
علاوه بر این، آبکاری میتواند به بهبود ویژگیهای ظاهری و زیبایی خودرو نیز کمک کند، که به نوبه خود تأثیر مثبتی بر تجربه کاربری دارد. خودروهایی که دارای قطعات آبکاری شده با کیفیت و جذاب هستند، معمولاً احساس لوکس بودن و کیفیت بیشتری را به راننده و سرنشینان منتقل میکنند. این ویژگیها میتوانند به رضایت مشتریان و افزایش فروش خودروها کمک کنند. در نتیجه، آبکاری نه تنها عملکرد فنی خودرو را بهبود میبخشد، بلکه به جذابیت و محبوبیت آن در بازار نیز میافزاید.
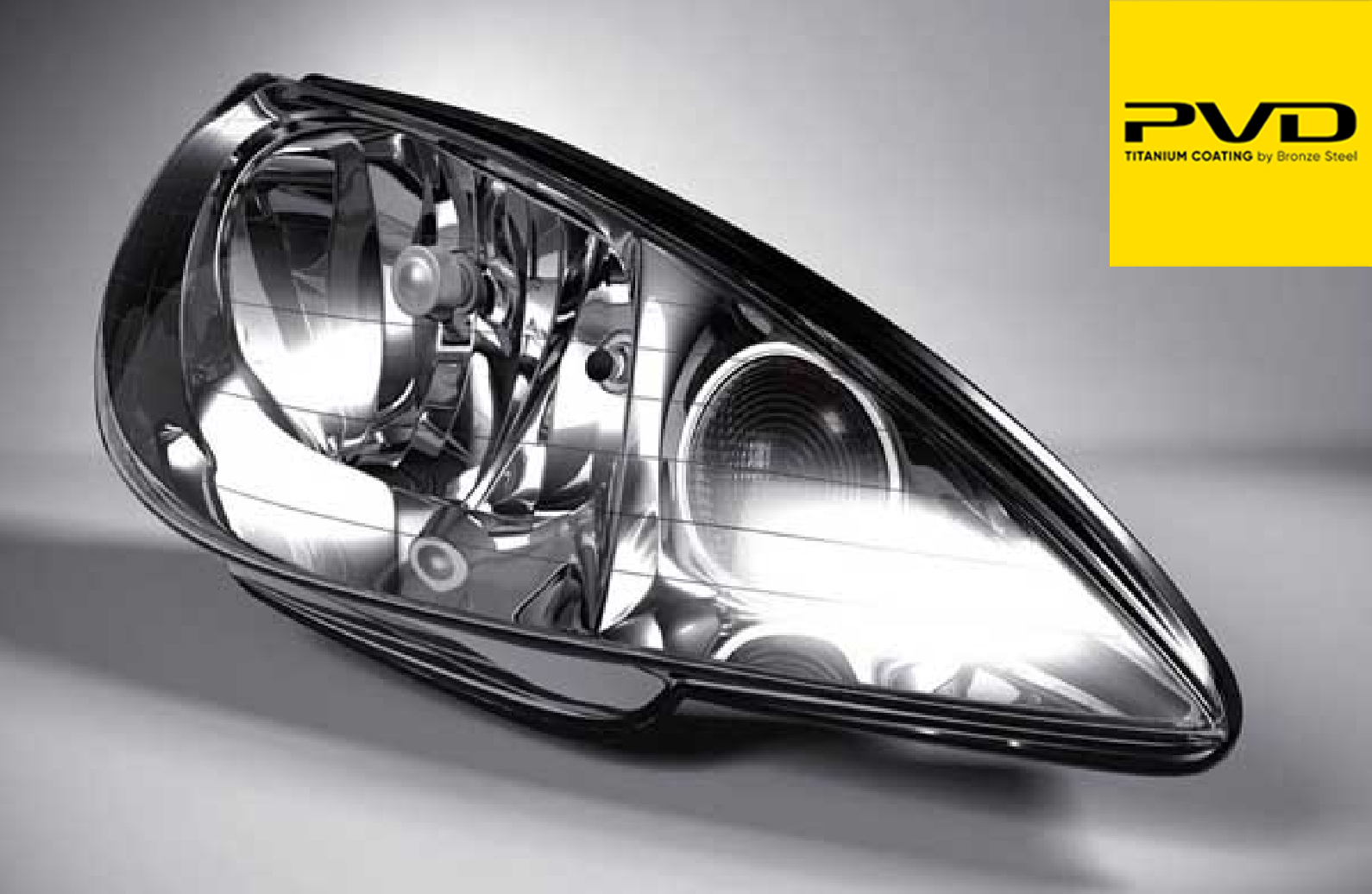
موانع و محدودیت های آبکاری در صنعت خودروسازی
آبکاری به عنوان یک فرآیند مهم در صنعت خودروسازی، مزایای زیادی دارد، اما همچنین با موانع و محدودیتهایی نیز همراه است. در ادامه به برخی از این موانع و محدودیتها اشاره میشود:
هزینههای بالا
فرآیندهای آبکاری میتوانند هزینهبر باشند، به ویژه هنگامی که از روشهای پیشرفته و مواد با کیفیت بالا استفاده میشود. تجهیزات مورد نیاز برای آبکاری، مواد شیمیایی و نیروی کار ماهر برای انجام این فرآیندها ممکن است هزینههای تولید را افزایش دهد. این امر میتواند به ویژه برای تولیدکنندگان کوچک و متوسط که به دنبال کاهش هزینهها هستند، یک چالش باشد.
مشکلات زیستمحیطی
آبکاری معمولاً شامل استفاده از مواد شیمیایی و فلزات سنگین است که میتوانند تأثیرات منفی بر محیط زیست داشته باشند. در صورت عدم مدیریت صحیح، این مواد میتوانند به آلودگی آب و خاک منجر شوند. به همین دلیل، تولیدکنندگان باید به رعایت قوانین و استانداردهای زیستمحیطی توجه داشته باشند و فرآیندهای آبکاری خود را به گونهای طراحی کنند که تأثیرات منفی را به حداقل برسانند.
محدودیت های فنی
برخی از روشهای آبکاری ممکن است برای قطعات خاص یا مواد خاص مناسب نباشند. به عنوان مثال، آبکاری بر روی برخی از آلیاژها یا مواد غیر فلزی ممکن است به خوبی عمل نکند و کیفیت پوشش را تحت تأثیر قرار دهد. همچنین، در برخی موارد، ضخامت لایههای آبکاری باید به دقت کنترل شود تا از ایجاد مشکلاتی مانند ترکخوردگی یا عدم چسبندگی جلوگیری شود. این محدودیتها میتوانند به پیچیدگی فرآیند تولید و نیاز به آزمایش و کنترل کیفیت بیشتر منجر شوند.
زمان بر بودن فرآیند
فرآیند آبکاری ممکن است زمانبر باشد، به ویژه در روشهایی که نیاز به مراحل چندگانه دارند. این امر میتواند به تأخیر در تولید و تحویل محصولات منجر شود و به عنوان یک مانع در پاسخگویی سریع به تقاضای بازار عمل کند. در نتیجه، تولیدکنندگان باید به دقت زمانبندی تولید و فرآیندهای آبکاری را مدیریت کنند تا از تأخیرات غیرضروری جلوگیری کنند.
نیاز به مهارت های تخصصی
آبکاری یک فرآیند پیچیده است که نیاز به تخصص و دانش فنی دارد. نیروی کار باید آموزش دیده و با فرآیندها و تجهیزات آشنا باشد تا کیفیت نهایی محصولات تضمین شود. کمبود نیروی کار ماهر میتواند به عنوان یک مانع برای تولیدکنندگان عمل کند و به کیفیت نهایی محصولات آسیب برساند.
اثرات بر روی خواص مکانیکی
در برخی موارد، فرآیند آبکاری میتواند بر خواص مکانیکی قطعات تأثیر بگذارد. به عنوان مثال، اگر لایه آبکاری به درستی کنترل نشود، ممکن است منجر به تغییر در خواص کششی یا سختی قطعه شود. این موضوع میتواند بر عملکرد نهایی خودرو تأثیر منفی بگذارد و منجر به شکستهای زودرس در قطعات شود.
این موانع و محدودیتها نشاندهنده چالشهای موجود در استفاده از تکنیکهای آبکاری در صنعت خودروسازی هستند و تولیدکنندگان باید به دقت این عوامل را در نظر بگیرند تا بتوانند از مزایای آبکاری به بهترین نحو بهرهبرداری کنند.
نتیجه گیری کیفیت خودرو با آبکاری
آبکاری به عنوان یک فرآیند حیاتی در صنعت خودروسازی، مزایای چشمگیری را به ارمغان میآورد. این مزایا شامل افزایش مقاومت در برابر خوردگی، بهبود ظاهر و زیبایی، افزایش سختی و مقاومت در برابر سایش، بهبود رسانایی الکتریکی و حرارتی و افزایش چسبندگی رنگ میباشند.
این فواید، منجر به افزایش طول عمر قطعات، بهبود عملکرد خودرو و کاهش هزینههای تعمیر و نگهداری میشوند. با این حال، آبکاری چالشهایی نیز به همراه دارد. نگرانیهای زیستمحیطی ناشی از استفاده از مواد شیمیایی سمی، هزینه بالای فرآیند و نیاز به کنترل کیفیت دقیق از جمله این چالشها هستند.
کاربرد انواع روش های آبکاری و پوشش pvd
صفر تا صد مراحل آبکاری قطعات موتور و خودرو
هلدینگ تبلیغاتی