آبکاری پلاستیک در صنایع هوافضا نقش مهمی در بهبود دوام و عملکرد قطعات دارد. این تکنیک با ایجاد لایهای محافظ روی پلاستیکها، مقاومت آنها را در برابر خوردگی، حرارت و سایش افزایش میدهد. وزن سبک پلاستیکها همراه با خواص بهبود یافته، آنها را به گزینهای ایدهآل برای استفاده در بخشهای حساس مانند سیستمهای الکترونیکی و پوششهای محافظ تبدیل کرده است.
آبکاری پلاستیک در صنایع هوافضا همچنین به بهینهسازی کارایی قطعات کمک میکند. در طراحی هواپیماها و فضاپیماها، این فرآیند علاوه بر حفظ وزن کم، باعث افزایش خواص الکتریکی و مقاومت در برابر شرایط سخت محیطی میشود. این ویژگیها به توسعه فناوریهای پیشرفته و ارتقاء ایمنی در این صنعت کمک شایانی میکنند.
تاریخچه آبکاری پلاستیک
تاریخچه آبکاری پلاستیک به دهه ۱۹۶۰ بازمیگردد، زمانی که این فناوری ابتدا در صنایع خودروسازی مورد استفاده قرار گرفت و به تدریج در سایر صنایع نیز کاربرد یافت. امروزه، آبکاری روی پلاستیک در محصولاتی مانند کفش، لپتاپ و تلفن همراه نیز بهکار میرود.
در ابتدا، خودروسازان به دنبال راهحلی برای کاهش مصرف سوخت بودند که نیاز به استفاده از قطعات سبک پلاستیکی را افزایش داد. آبکاری پلاستیک بهمنظور ایجاد ظاهری فلزی و جذاب بر روی این قطعات توسعه یافت. یکی از مهمترین دستاوردها در این مسیر، ابداع فرآیندی شیمیایی برای اتصال میان سطح پلاستیکی و اکریلونیتریل بوتادین استایرن (ABS) بود، مادهای ترموپلاستیک که به دلیل مقاومت بالای خود در برابر ضربه بسیار مناسب این روش است. این فرآیند، چسبندگی مطلوبی بین ABS و پوشش فلزی ایجاد میکرد.
جالب است بدانید که آبکاری پلاستیک در دهه ۱۹۶۰ به سرعت رشد کرد و در دهه ۱۹۷۰ صنایعی مانند لولهکشی و الکترونیک نیز به مزایای آن پی بردند. با این حال، تغییرات در صنعت خودروسازی و کاهش تقاضا برای پوششهای براق در دهه ۱۹۹۰ موجب افت استفاده از این فناوری شد.
طی سالهای اخیر، با بهبود کیفیت آبکاری پلاستیک و افزایش تقاضا در بخشهای مختلف صنایع، این فناوری مجدداً در بازارهای آمریکای شمالی و اروپا جایگاه خود را بازیافته است و بهعنوان روشی کاربردی و نوآورانه شناخته میشود.
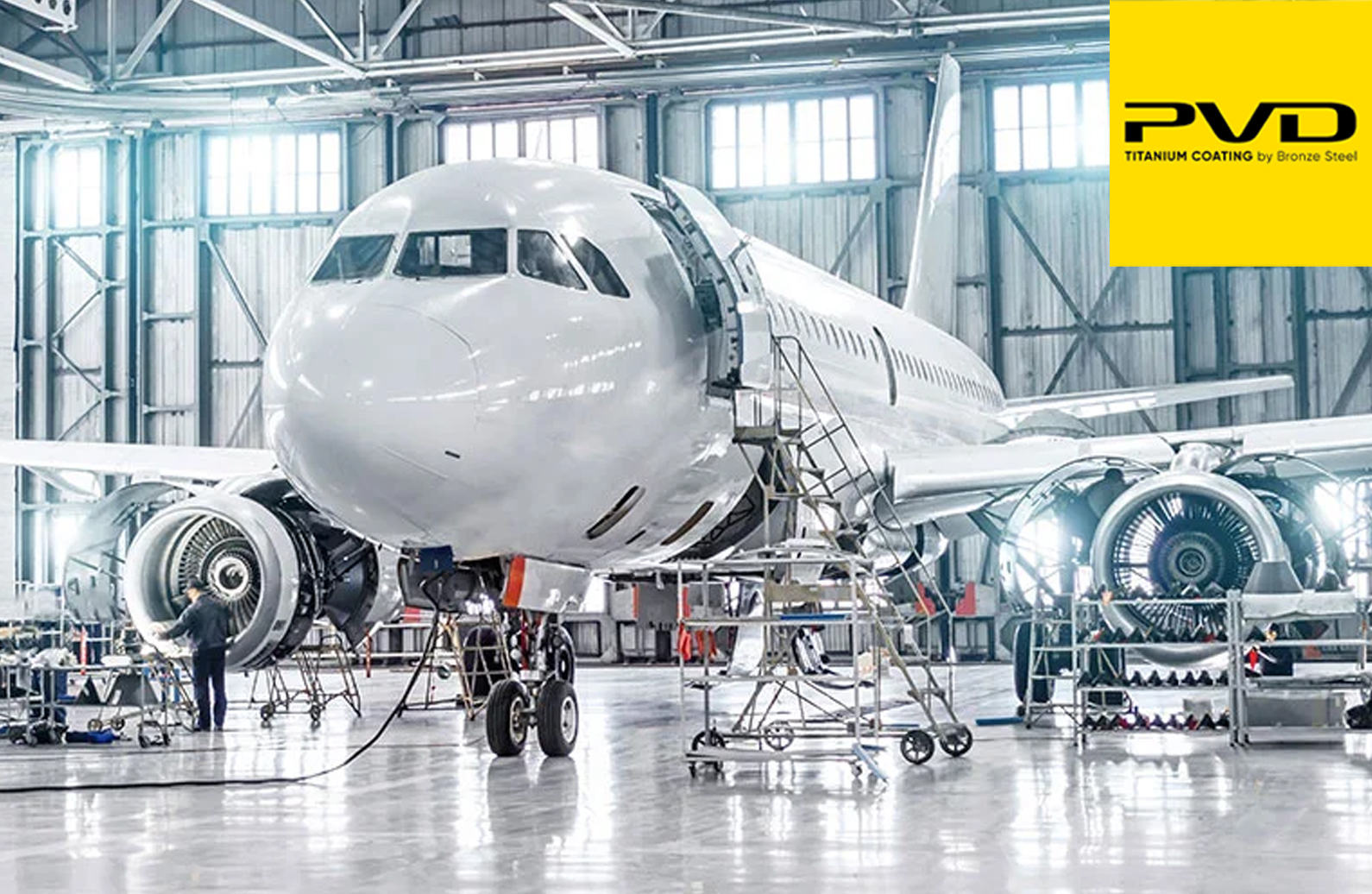
مهم ترین کاربردهای آبکاری پلاستیک
صنعت خودروسازی
پلاستیکها به دلیل وزن سبک و انعطافپذیری، حدود ۱۵-۲۰ درصد قطعات داخلی و خارجی خودروها را تشکیل میدهند. آبکاری نیکل روی بخشهایی مثل جلوپنجره، دستگیرهها و ضربهگیرها برای جذابیت بیشتر انجام میشود.
صنعت الکترونیک
آبکاری پلاستیک در قطعات موبایل، کامپیوتر و کلیدهای کنترل کاربرد دارد. این فرآیند علاوه بر بهبود ظاهر، باعث رسانایی الکتریکی و حفاظت در برابر عوامل محیطی میشود.
لولهکشی
لولهها و ابزارهای پلاستیکی آبکاریشده با نیکل یا طلا، ظاهر براق و کیفیت بالایی برای حمام و آشپزخانهها فراهم میکنند.
سایر کاربردها
- محصولات مقاوم به حرارت: شیلد گرمایی برای قطعات در معرض دمای بالا
- محصولات رادیویی: آنتنها و فیلترهای RF
- محصولات بهداشتی: اتصالات دوش و لوازم آشپزخانه با قابلیت پاکسازی آسان
- محصولات خانگی: دستگیرهها و کنترلهای آبکاریشده
- پوشاک: دکمههای فلزینما
- درب بطریها: بطریهای عطر با دربهای براق برای جلوهای لوکس
مبانی فرآیند آبکاری پلاستیک
برای آمادهسازی پلاستیک پیش از آبکاری، قطعات باید قالببندی و تمیز شوند تا از هرگونه نقص سطحی و آلودگی پاک شوند. از آنجایی که پلاستیک مادهای غیرفلزی است، نیاز به فرآیند متالیزه کردن دارد تا چسبندگی لایه فلزی بهبود یابد. این کار اغلب با آبکاری الکترولس انجام میشود که در آن فلز بدون جریان الکتریکی روی پلاستیک رسوب میکند.
مراحل آبکاری الکترولس روی پلاستیک
- شستشو: حذف آلودگیها با چربیگیر قلیایی یا محلول اسید کرومیک.
- پیشحمام: افزایش قابلیت چسبندگی سطح پلاستیک با حلالهای اچکننده.
- اچینگ: ایجاد حفرههای میکروسکوپی با تریاکسید کروم یا اسید سولفوریک برای بهبود چسبندگی فلز.
- خنثیسازی: حذف مواد اضافی با بیسولفیت سدیم.
- پیشفعالسازی: آمادهسازی سطح برای جذب بهتر فعالکنندهها.
- فعالسازی: افزودن فلزات کاتالیزور مانند پالادیوم یا پلاتین.
- شتابدهی: جلوگیری از پوشش نامنظم و بهبود عملکرد کاتالیزور.
- غوطهوری در حمام: رسوب نیکل یا مس برای ایجاد سطح هادی جریان.
انواع آبکاری الکترولس پلاستیک
- آبکاری سراسری: پوشش فلزی یکنواخت با ضخامت 1 تا 50 میکرون؛ مقرونبهصرفهترین روش.
- آبکاری انتخابی: پوششدهی بخشهای خاص با دقت بالا و ضخامت 1 تا 10 میکرون؛ مناسب برای کاربردهای حساس.
تکنیکهای پیشرفته در آبکاری پلاستیک برای هوافضا
صنایع هوافضا به دلیل نیاز به قطعاتی سبک، بادوام و مقاوم، همواره از فناوریهای پیشرفته برای تولید بهره میگیرد. در این میان، آبکاری پلاستیک بهعنوان یک فناوری مؤثر، نقش مهمی در تحقق این اهداف دارد. این روش با افزودن لایههای فلزی روی مواد پلاستیکی، ویژگیهای مکانیکی، حرارتی و الکتریکی قطعات را بهبود میبخشد و وزن آنها را کاهش میدهد.
کاهش وزن و افزایش کارایی
در صنایع هوافضا، کاهش وزن از اولویتهای اصلی محسوب میشود، زیرا هر گرم اضافی هزینههای پرتاب و مصرف سوخت را افزایش میدهد. آبکاری پلاستیک امکان تولید قطعات سبک پلاستیکی با خواص فلزی را فراهم میکند. برای مثال، قطعاتی مانند تزئینات داخلی کابین هواپیما، سنسورها و محفظههای الکترونیکی، با استفاده از این روش وزن کلی هواپیما را کاهش داده و همزمان استحکام لازم را حفظ میکنند.
مقاومت در برابر شرایط سخت
قطعات مورد استفاده در صنایع هوافضا باید توانایی مقابله با شرایط دشوار محیطی مانند دماهای بالا یا پایین، فشارهای متغیر و تابش اشعههای کیهانی را داشته باشند. آبکاری پلاستیک با اضافه کردن لایههایی از فلزات مقاومی مانند نیکل، کروم یا آلومینیوم، مقاومت قطعات را افزایش میدهد و طول عمر آنها را بیشتر میکند. این ویژگی باعث کاهش نیاز به تعمیر یا تعویض مکرر قطعات میشود.
ویژگیهای الکتریکی و حرارتی
برخی قطعات هوافضا نیازمند رسانایی الکتریکی یا هدایت حرارتی مناسب هستند. آبکاری پلاستیک با استفاده از فلزاتی مانند مس یا نقره، این خواص را به قطعات پلاستیکی میافزاید. قطعاتی که با این روش تولید میشوند، به دلیل سبکی و کارایی بالا در سیستمهای حساس هوافضا کاربرد گستردهای دارند.
صرفهجویی در هزینه و حفظ محیطزیست
آبکاری پلاستیک در مقایسه با تولید قطعات فلزی کامل، هزینههای تولید را کاهش داده و امکان بازیافت قطعات را فراهم میکند. این موضوع علاوه بر کاهش ضایعات، به پایداری زیستمحیطی کمک میکند. در پروژههای فضایی که کاهش اثرات زیستمحیطی اهمیت زیادی دارد، این فناوری بسیار مورد توجه قرار میگیرد.
کاربردهای گوناگون در صنایع هوافضا
- محفظههای الکترونیکی: افزایش مقاومت در برابر تداخلات الکترومغناطیسی.
- سنسورها و تجهیزات حساس: بهبود دقت و دوام.
- قطعات داخلی هواپیما: طراحی سبک، مقاوم و زیبا برای کابین.
آبکاری پلاستیک با ترکیب مزایای پلاستیک و فلز، در تولید قطعات سبک و بادوام برای صنایع هوافضا نقش کلیدی دارد. این فناوری ضمن ارتقای عملکرد قطعات، هزینهها را کاهش داده و به حفظ محیطزیست کمک میکند. با پیشرفت تکنولوژی، انتظار میرود این روش کاربرد گستردهتری در آینده داشته باشد و به رکن اساسی تولید قطعات هوافضایی تبدیل شود.
مواد مناسب برای آبکاری پلاستیک
در حالی که ABS همچنان در 90 درصد آبکاریهای پلاستیک استفاده میشود، رزینهای دیگری نیز بهطور مؤثر برای پوششدهی کاربرد دارند. این رزینها شامل فنولیک، اوره فرمآلدهید، پلیاتر سولفون، دیآلیل فتالات، پلیاتر ایمید، تفلون، پلیآریل اتر، پلیکربنات، پلیفنیلن اکساید، نایلون سخت معدنی و پلیسولفون هستند.
پلاستیکهایی که بهعنوان “قابل آبکاری” شناخته نمیشوند، مانند رزینهای پلیاستر (شامل پلیاتیلن، پلیاستر و PVC)، نیز قابل پوششدهی هستند. برخی پلاستیکها مانند خانواده نوریلها، اورتان، پلیپروپیلن، PEEK و PPS تنها بهصورت ترکیبی آبکاری میشوند. بهطور کلی، هرچه مقاومت شیمیایی رزین بالاتر باشد، فرآیند آبکاری دشوارتر خواهد بود.
از میان فلزات قابل استفاده، مس برای کاربردهای هدایت الکتریکی محبوب است. فلزات دیگر شامل کروم، طلا، نقره و نیکل بوده و گاهی از لایههای ترکیبی فلزات استفاده میشود.
مزایای آبکاری پلاستیک در صنایع هوافضا
آبکاری پلاستیک در صنایع هوافضا مزایای چشمگیری مانند کاهش وزن، بهبود مقاومت به شرایط سخت، افزایش رسانایی الکتریکی و حرارتی، و کاهش هزینههای تولید دارد. این فناوری با ایجاد لایههای فلزی روی پلاستیک، کارایی و دوام قطعات را افزایش میدهد و نیاز به تعمیرات مکرر را کاهش میدهد.
افزایش محدودیت در استفاده از پلاستیک و کامپوزیتهای آن، تقاضا برای آبکاری پلاستیک را بیشتر کرده است. این روش علاوه بر بهبود ظاهر و ایجاد حس کیفیت، سطح پلاستیک را در برابر خوردگی، مواد شیمیایی و نور مقاوم میکند و حتی پایداری آن را افزایش میدهد.
سایر مزایا:
- کاهش مصرف سوخت
- بهبود ظاهر قطعات
- افزایش مقاومت در برابر خوردگی
- کاهش اثرات زیستمحیطی
- قابلیت بازیافت و استفاده مجدد
اهمیت آبکاری پلاستیک در تولید قطعات الکترونیکی هوافضا
آبکاری پلاستیک در تولید قطعات الکترونیکی هوافضا نقش کلیدی ایفا میکند. این فناوری با ایجاد رسانایی الکتریکی روی پلاستیک، امکان استفاده از مواد سبک و مقاوم را در مدارهای پیچیده فراهم میسازد. قطعات الکترونیکی با پوشش فلزی از مقاومت بیشتری در برابر شرایط محیطی سخت مانند دماهای بالا، تابش اشعه و رطوبت برخوردار میشوند که در صنعت هوافضا ضروری است.
همچنین، آبکاری پلاستیک باعث افزایش دوام قطعات و بهبود عملکرد سیستمهای الکترونیکی میشود. از سوی دیگر، این فرآیند قابلیت اتصال لحیمکاری مستقیم بر روی بلوکهای متصلکننده را ممکن میسازد و به کاهش وزن کلی تجهیزات کمک میکند. در نتیجه، قطعات الکترونیکی هوافضا با کیفیت بالاتر و کارایی بیشتر تولید میشوند.
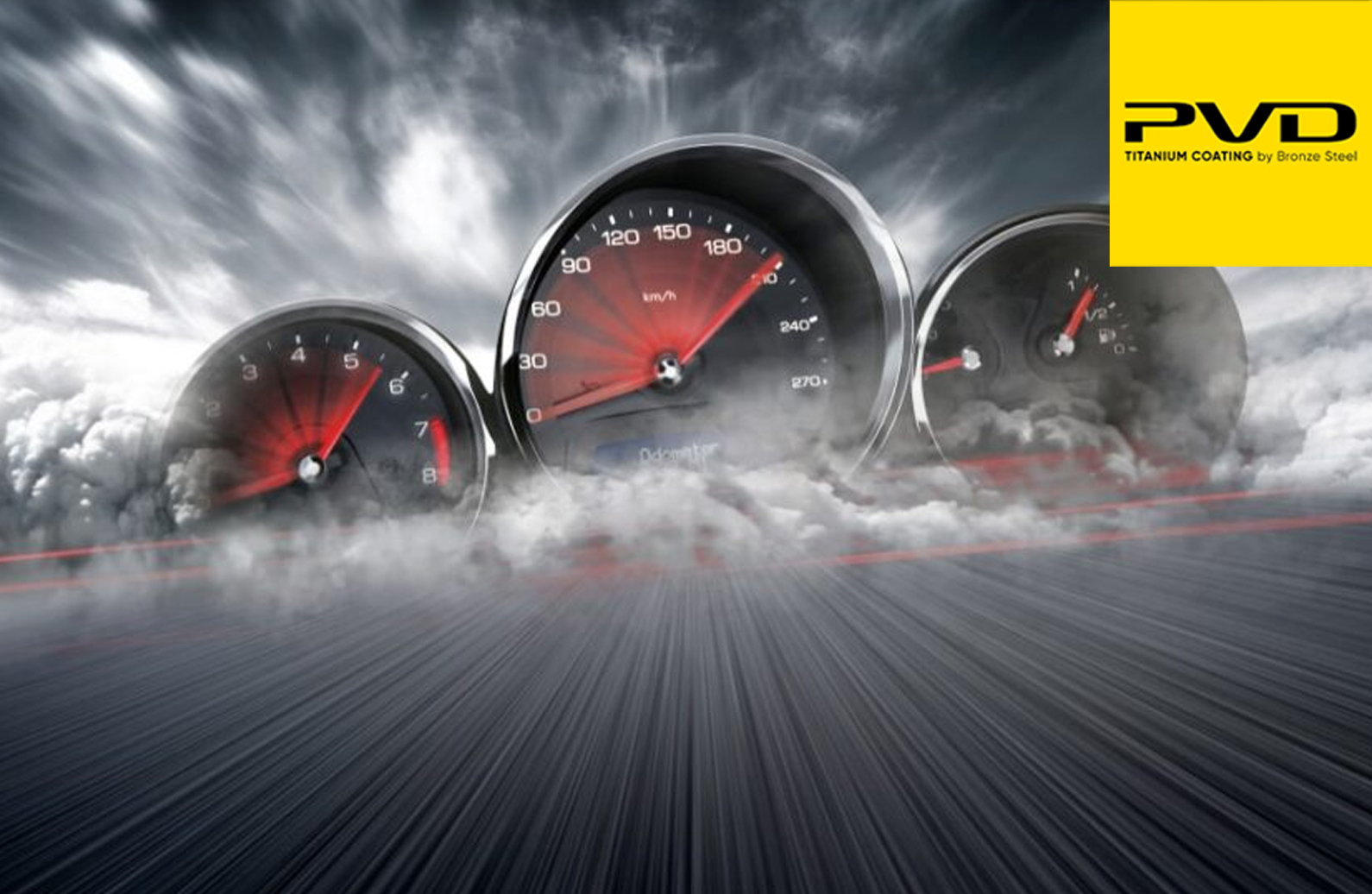
مقایسه آبکاری پلاستیک با سایر روشهای پوششدهی
آبکاری پلاستیک در مقایسه با سایر روشهای پوششدهی مانند رنگآمیزی یا پوششهای پودری، از ماندگاری و دوام بیشتری برخوردار است. این فرآیند با ایجاد لایهای فلزی روی پلاستیک، علاوه بر افزایش مقاومت در برابر خوردگی و سایش، ظاهر براق و باکیفیتی به قطعات میدهد. برخلاف رنگآمیزی که ممکن است در طول زمان پوسته شود، آبکاری به دلیل اتصال شیمیایی قویتر، پایدارتر است.
از نظر عملکرد، آبکاری پلاستیک قابلیتهایی مانند رسانایی الکتریکی و مقاومت در برابر گرما را فراهم میکند که در روشهای دیگر معمولاً امکانپذیر نیست. همچنین، این روش به کاهش وزن قطعات نسبت به استفاده از فلزات سنگین کمک میکند. هرچند فرآیند آبکاری نسبت به روشهای دیگر هزینهبرتر است، اما مزایای کاربردی و زیبایی آن در صنایع پیشرفته، توجیه اقتصادی بالایی دارد.
کاربردهای آبکاری پلاستیک در طراحی قطعات هوافضا
آبکاری پلاستیک در طراحی قطعات هوافضا به کاهش وزن، افزایش مقاومت در برابر خوردگی و بهبود خواص ظاهری کمک میکند. این فناوری باعث تقویت قطعات پلاستیکی با لایههای فلزی میشود که علاوه بر افزایش استحکام، خواص رسانایی الکتریکی و حرارتی را نیز فراهم میآورد.
- قطعات الکترونیکی: بهبود رسانایی الکتریکی در سیستمهای ارتباطی.
- عایق حرارتی: محافظت قطعات در برابر دماهای شدید.
- طراحی داخلی هواپیما: زیباسازی و افزایش دوام قطعات پلاستیکی.
- سیستمهای راداری: بهبود عملکرد تجهیزات رادیویی و موجبرها.
- سازههای سبکوزن: کاهش وزن با حفظ مقاومت مکانیکی.
نکته نهایی در مورد آبکاری پلاستیک در صنایع هوافضا
آبکاری پلاستیک در صنایع هوافضا بهویژه در تولید قطعات دقیق و حساس مانند اجزای سیستمهای الکترونیکی و ارتباطی، نقش بسیار مهمی دارد. این فرآیند بهویژه در افزایش مقاومت و هدایت الکتریکی قطعات پلاستیکی بسیار مفید است. در صنعت هوافضا، مقاومت در برابر شرایط محیطی مانند حرارت، فشار و رطوبت از اهمیت بالایی برخوردار است. شرکت ایران برنز استیل با ارائه خدمات تخصصی آبکاری پلاستیک میتواند به تولید قطعاتی کمک کند که این استانداردهای سخت را بهخوبی رعایت کرده و عملکرد مطلوبی داشته باشند.
علاوه بر این، آبکاری پلاستیک در صنایع هوافضا به کاهش وزن و هزینههای تولید کمک میکند. با استفاده از مواد پلاستیکی سبک وزن و مقاوم در برابر خوردگی که بهوسیله فلزات مختلف آبکاری میشوند، تولیدکنندگان قادر خواهند بود قطعات با ویژگیهای عالی تولید کنند بدون اینکه بهطور قابلتوجهی بر روی وزن کلی تأثیر بگذارند. شرکت ایران برنز استیل بهعنوان یک پیشگام در این صنعت، با استفاده از فناوریهای پیشرفته خود، قادر است به طراحی و تولید قطعات هوافضا با کیفیت و دقت بالا کمک کند.
نقش فناوری نانو در ارتقای آبکاری پلاستیک و بهبود ویژگیها
اولین و بزرگترین مرکز خدمات آبکاری خلا یا پی وی دی
هلدینگ تبلیغاتی